Recent experimental developments on a semi-active stiffness control device to suppress vibrations – The Smart Spring
At LMSSC, Cnam, Paris, December 14th 2011, 11 a.m.
Fred Nitzsche
Professor, Department of Mechanical and Aerospace Engineering, Rotorcraft Research Group, Carleton University, Ottawa, Canada
Professor, Department of Mechanical and Aerospace Engineering, Rotorcraft Research Group, Carleton University, Ottawa, Canada
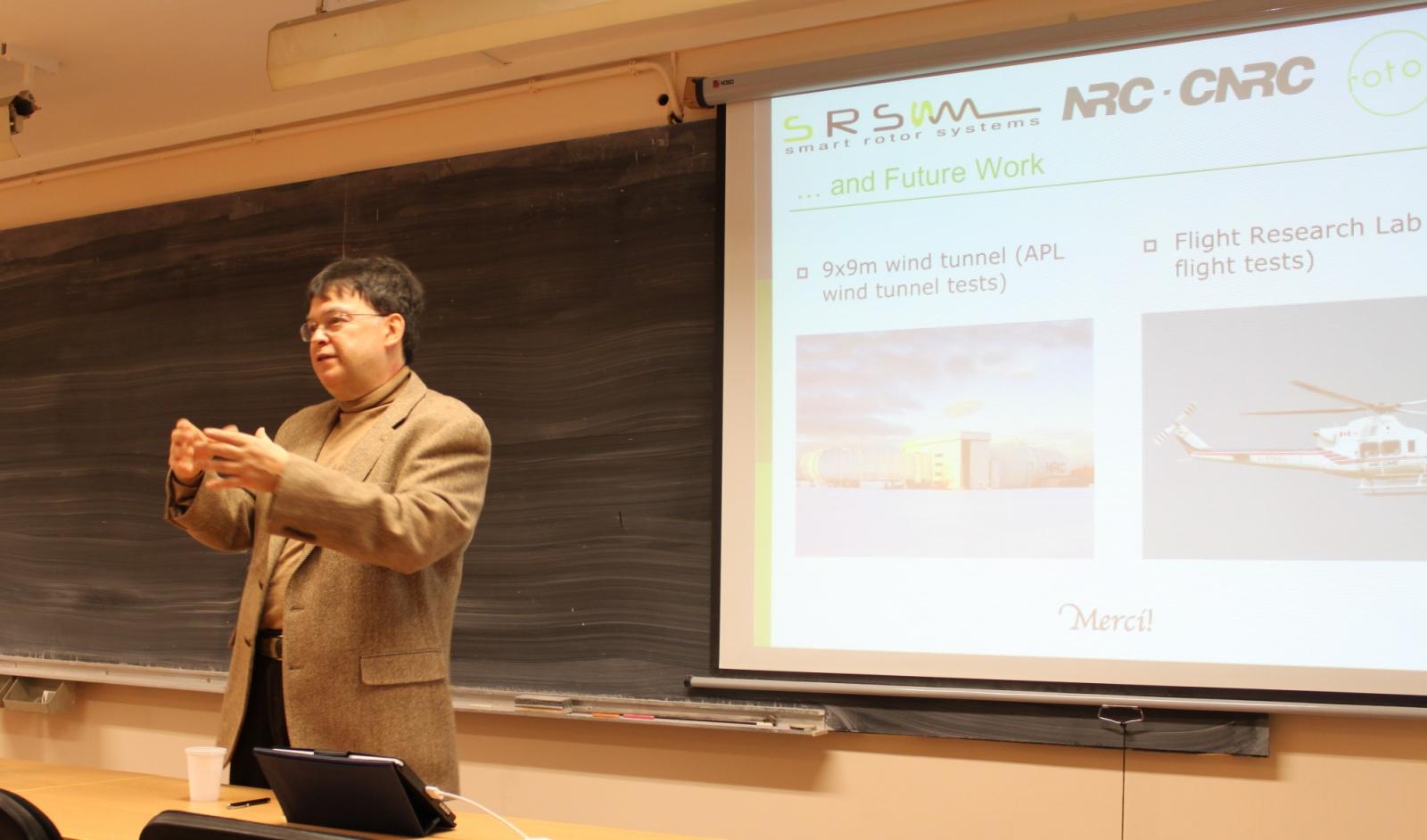
The Smart Spring concept is a semi-active approach to vibration suppression that makes use of an actively tunable impedance device. The large bandwidth and force generating capabilities of the piezoelectric actuators are exploited while the relatively large power requirement often associated with other active approaches is circumvented. It has been demonstrated that the Smart Spring device is capable of controlling all aspects of the complex impedance of a dynamic system. The Smart Spring is also capable of controlling both the damping and resonance frequencies exhibited by any complex dynamic system in which it can be integrated, such as the dynamic response of continuous structures. Numerical simulations and tests have demonstrated that the Smart Spring, in conjunction with a feedback controller, achieved significant vibration suppression; particularly in frequency bands near the system resonance frequencies. Although it has been established that the Smart Spring is capable of continuously varying the dynamic impedance characteristics of a dynamic system, an on-off state-switch-type control was chosen for the sake of demonstration. The state-switch controller is based on principles of maximum energy extraction and predominantly makes use of controlled damping effects. The experimental results indeed show that a controlled variation in the dynamic impedance of the Smart Spring can be used to achieve significant vibration suppression in the hosting structure, especially if it is located in a region of high stresses such as at the root of a wing. This suppression occurs over multiple, relatively wide frequency bands and the peak suppression occurs at the baseline resonance frequencies where anti-resonance peaks are produced.
The Smart Spring is now patented in US and in Europe as a solid-state actuator device made from “smart” materials, which converts the energy into mechanical work. The actuation work is not performed against the external loads but rather internally to the structure, saving actuation power.
The present applied research program pursued with the Smart Spring is the attenuation of forced vibration generated in rotorcraft blades by the unsteady aerodynamic loads, which is recognized to be one of the most demanding applications for this device. Although the proof-of-concept of the Smart Spring was successfully tested at the facilities of the National Research Council of Canada in 2002, these tests were preformed under non-rotating conditions, in the absence of the huge centrifugal loads that dominate the rotorcraft blades environment. Hence, several problems remained to be solved in order to test a prototype of the Smart Spring in an actual helicopter rotor environment. These problems resided mainly in the area of materials research, piezoelectric material modeling, characterization and functional reliability. Recently, this research has proceeded into a third generation of prototypes (Fig. 1) and the tests were performed in the new whirl-tower facility at Carleton University (Fig. 2). This paper will summarize the most recent achievements of this research.
![]() Fig. 1 :
Smart Spring prototype third-generation
|
![]() Fig. 2 : New whirl-tower facility at Carleton University
|